The Lean Champion
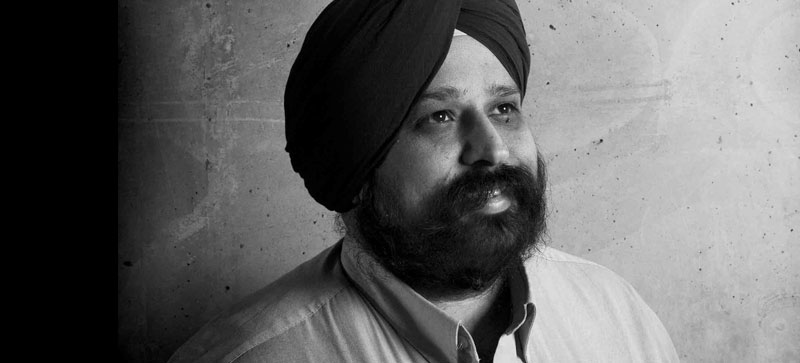
University Hospital’s inpatient pharmacy technician supervisor Raghbir Makhar was always looking for ways to optimize the processes that were around him. What he was missing was a framework to systematically implement some of his ideas. After attending a performance excellence training workshop, where he learned about Lean tools and techniques, he became unstoppable. “It’s like his inner Leanness has been unleashed,” says Linda Tyler, Pharm.D., professor (clinical), associate dean of pharmacy and the administrative director of pharmacy services. “He’s on a relentless quest to make everything more efficient.”
He went on to study an advanced Lean curriculum and with the support of a project mentor, Makhar began to envision efficiencies across the system. “I realized we were all doing the same processes a little bit differently,” he explains. “And we were a little too accepting of the resulting chaos and errors.” Using Lean methodologies Makhar analyzed what each tech did every day, and then engaged the techs in creating more than 100 standard operating procedures. “I didn’t do it,” he says. “It’s the team.” They created a streamlined medication cart fill process, standardized training, and increased automation for an expensive robot used for drug packaging. His vigilance about managing drugs has suppliers questioning why there are no expired drugs to pick up. It’s about the discipline of “always.”
“If we want to keep patients safe, we need to do it right 100 percent of the time,” says Makhar.
Change didn’t happen overnight. “Initially there were people who said it wouldn’t work,” recalls Makhar. “I had to keep explaining how the new processes would save us money and keep patients safer.” With Makhar’s dogged persistence, he’s found new standardizations for even the smallest pharmacy tasks. One project alone has freed up more than 250 hours of technician time per year and saved the pharmacy more than $30,000 in labor, drug and supply costs, not to mention the avoidance of other costs and dangerous medical errors.
Makhar is making a difference one task at a time, saving money and improving quality. “We don’t have to wait for a million-dollar project to come along,” says Sandi Gulbransen, value engineering manager and Lean educator. “If everyone in our institution improves where they can, and focuses on the things they can control, we have the power to really change things.”